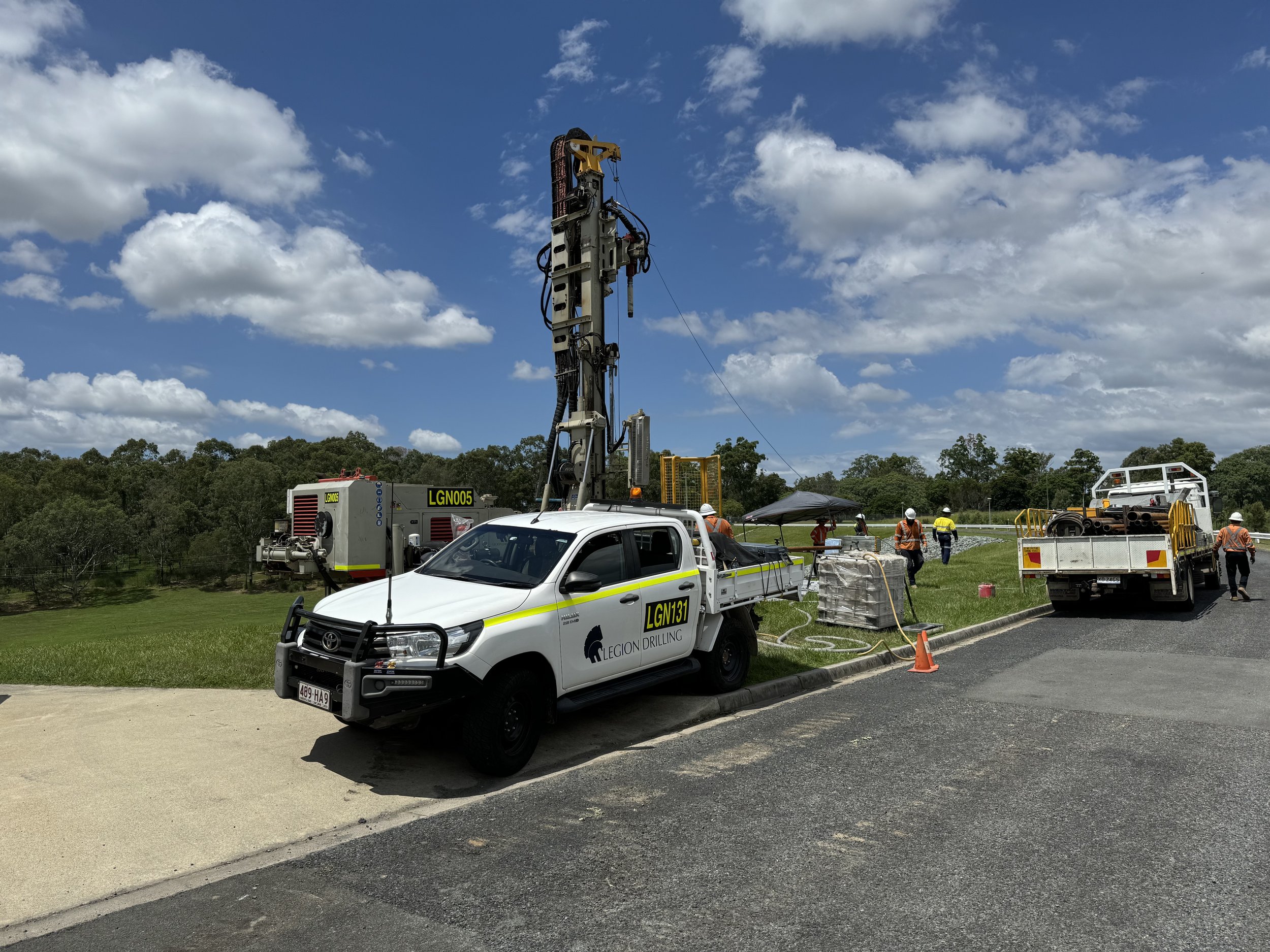
Vibrating Wire Piezometer Installation
Vibrating Wire Piezometers
Pore Pressure Monitoring
When installing Vibrating Wire (VW) piezometers for pore pressure monitoring, it’s crucial to work with a drilling contractor who has the appropriate expertise and experience. The success and longevity of the installation depend on careful planning, precise execution, and adherence to best practices. Ensuring that the drilling contractor has a proven track record in geotechnical installations can significantly reduce the risk of issues during the installation process and improve the reliability of long-term monitoring.
Legion Drilling offers extensive experience in the installation of VW piezometers, backed by our professional team and advanced equipment. With depots in Brisbane, Sydney, and Townsville, we provide specialized drilling services across various regions, ensuring that your monitoring systems are installed correctly and maintained for optimum performance.
How Vibrating Wire Piezometers Work
VW piezometers can be installed in boreholes, open wells, or embedded in fill materials. They feature a magnetic coil and a tensioned wire connected to a diaphragm. When the wire is excited by the magnetic coil, it vibrates at a frequency determined by its tension. This frequency signal is processed, converted into a pressure value (pore pressure), and stored in a data logger for analysis.
Selecting Ranges for Vibrating Wire Piezometers
When selecting ranges for vibrating wire piezometers, it is critical to balance precision and durability based on your project requirements and site conditions. These instruments measure pore water pressure and are widely used in geotechnical and hydrological applications, including dam monitoring, slope stability analysis, and groundwater studies.
The first step is understanding the expected range of pressures at the installation site. Choose a piezometer with a pressure range slightly higher than the maximum expected pore pressure. Over-specifying the range may reduce accuracy, while under-specifying could lead to overloading and instrument failure. For shallow installations, low-pressure models (e.g., 0-500 kPa) offer higher resolution, whereas deeper installations might require ranges up to 10 MPa or more.
Additionally, consider the project environment. For corrosive or high-temperature conditions, ensure the device is made from suitable materials like stainless steel or titanium. If rapid pressure fluctuations are expected, select models with high frequency response capabilities.
Lastly, match the piezometer’s range with the data logger or readout device for seamless integration. Regular calibration and validation are essential to maintain accuracy and reliability. Proper selection ensures your piezometers provide precise data, enabling informed decisions for project safety and performance.
Why Use a Vibrating Wire Piezometer Over a Monitoring Well?
Vibrating wire piezometers offer distinct advantages over traditional monitoring wells, particularly in projects requiring precise, real-time data and minimal environmental impact. Here's why they are often the preferred choice:
Precision and Sensitivity
Vibrating wire piezometers deliver highly accurate and sensitive measurements of pore water pressure, even in small or rapid pressure fluctuations. Monitoring wells, in contrast, provide water level measurements that may require manual conversion to estimate pressure, which can introduce errors.Real-Time Data Collection
Piezometers can be integrated with data loggers for continuous, automated monitoring, allowing for real-time insights. Monitoring wells typically require manual readings, which can delay data collection and analysis.Site Accessibility
Piezometers are ideal for installations in difficult-to-access locations, such as steep slopes, embankments, or underground tunnels. Monitoring wells, with their larger footprint and requirement for regular access, may be impractical in such conditions.Environmental Impact
Piezometers have a smaller installation footprint and are less invasive compared to drilling and maintaining a monitoring well. This reduces the risk of contamination and minimizes disturbance to the surrounding environment.Durability in Challenging Conditions
Designed for harsh environments, vibrating wire piezometers are resistant to high pressures, corrosive conditions, and extreme temperatures. Monitoring wells are more vulnerable to environmental damage and require frequent maintenance.Cost and Efficiency
While piezometers may have higher initial costs, their low maintenance requirements and automation capabilities make them cost-effective over time, especially for long-term or large-scale projects.
In summary, vibrating wire piezometers provide precise, reliable, and efficient pore water pressure monitoring, making them an excellent choice for applications where accuracy, real-time data, and minimal environmental impact are crucial.
Installation Methodologies for VWP
Proper installation of Vibrating Wire piezometers is crucial for obtaining accurate and reliable data. Below are some best practices:
Site Preparation:
Conduct a thorough site assessment to determine optimal sensor placement.
Ensure borehole or well dimensions are appropriate for the piezometer design.
Pre-Installation Testing:
Calibrate the piezometer to verify accurate readings before installation.
Perform a functional test to ensure no damage occurred during transportation.
Grouting and Sealing:
Use bentonite-cement grout for grouting-in the piezometer to prevent fluid migration.
Seal the borehole to maintain isolation of the monitoring zone.
Cable Protection:
Route cables carefully to avoid damage during and after installation.
Use protective conduits or cable guards where necessary, especially in high-traffic areas.
Data Logger Configuration:
Connect the piezometer to a compatible data logger.
Configure the logger to capture data at appropriate intervals for the project’s objectives.
Post-Installation Verification:
Conduct a series of initial readings to verify proper installation.
Monitor data trends to identify any inconsistencies or anomalies.
Documentation and Reporting:
Maintain detailed installation records, including sensor depth, grout mix, and calibration data.
Regularly inspect the installation site for any signs of disturbance.
Common Issues with Vibrating Wire Piezometer Installation
While Vibrating Wire piezometers offer precise data collection, there are several issues that may arise during installation:
Poor Cable Protection:
Cables that are not properly shielded or protected from mechanical damage can lead to signal loss or degradation, affecting data accuracy.
Solution: Use protective conduit or cable guards, and ensure cables are routed through areas where they won’t be subjected to external forces.
Incorrect Grouting:
Improper grouting can result in poor contact between the piezometer and the surrounding soil, leading to inaccurate readings.
Solution: Use high-quality bentonite-cement grout, ensuring thorough mixing and proper sealing of the borehole.
Faulty Calibration:
Incorrect calibration of the piezometer prior to installation can lead to inaccurate pressure readings.
Solution: Perform calibration tests to verify sensor accuracy before installation, and document calibration results.
Installation Depth Issues:
Installing the piezometer at the wrong depth or in an unsuitable geological zone can result in irrelevant or misleading data.
Solution: Carefully assess the geological profile of the site to determine the optimal depth for installation.
Temperature Sensitivity:
Temperature fluctuations can affect the vibration frequency of the wire, causing measurement errors.
Solution: Ensure proper placement of temperature sensors, or use piezometers with built-in temperature compensation features to mitigate this issue.
Borehole Instability:
Borehole collapse or instability during installation can compromise the piezometer’s position and data reliability.
Solution: Use borehole stabilization techniques and equipment to maintain borehole integrity during installation.
Signal Interference:
External electromagnetic interference can affect the transmission of the VW signal, leading to incorrect readings.
Solution: Use shielded cables and avoid routing cables near sources of electromagnetic interference.
Benefits of Vibrating Wire Piezometers
Reliable signal transmission: Shielded cables ensure long-distance data integrity.
Accurate and repeatable readings: Ideal for long-term monitoring.
Groutable design: Can be directly grouted-in using bentonite-cement grout.
Temperature monitoring: Equipped with built-in temperature sensors.
Automated data collection: Compatible with data loggers for continuous monitoring.
VW piezometers are available in various designs to accommodate diverse applications and ground conditions, ensuring tailored solutions for each project.
Drive-Point Piezometers: Overview and Applications
What Are Drive-Point Piezometers?
Drive-point piezometers, also known as push-in or direct-push piezometers, are small-diameter, temporary or semi-permanent monitoring wells used to measure groundwater pressure, flow, and quality at various depths. They are typically made of stainless steel or PVC and consist of a screened tip attached to a hollow pipe, which is driven into the subsurface using a manual slide hammer, direct-push rig, or percussion hammer.
When Are Drive-Point Piezometers Used?
Shallow Groundwater Monitoring
Ideal for measuring groundwater levels and hydraulic gradients in shallow aquifers and near-surface sediments.
Hydrogeological Investigations
Used in site characterization for contaminated sites, landfill leachate monitoring, and wetland hydrology studies.
Helps determine water table fluctuations, flow direction, and recharge/discharge zones.
Environmental Site Assessments (ESAs)
Commonly used in Phase II ESAs to assess potential petroleum hydrocarbon, solvent, or heavy metal contamination in soil and groundwater.
Temporary Groundwater Sampling
Enables rapid collection of groundwater samples for contaminant analysis without the need for permanent well installation.
In Situ Remediation Monitoring
Used to monitor the effectiveness of in situ remediation technologies (e.g., activated carbon injections, chemical oxidation, and bioremediation).
Helps track contaminant degradation, amendment distribution, and geochemical changes over time.
Streambed & Surface Water-Groundwater Interaction Studies
Used in riparian and wetland studies to assess interactions between surface water and groundwater flow.
Helps identify seepage zones, hyporheic flow, and seasonal water table fluctuations.
Advantages of Drive-Point Piezometers
✅ Fast & Cost-Effective – Quick installation compared to traditional monitoring wells
✅ Minimal Site Disturbance – No need for drilling or heavy equipment
✅ Versatile & Portable – Can be used in remote or difficult-to-access locations
✅ Ideal for Temporary Monitoring – Easily removed after data collection
Limitations of Drive-Point Piezometers
❌ Limited to Shallow Applications – Typically not suitable for deep aquifers (>10-15 meters depth)
❌ Potential for Smearing – May cause compaction of fine sediments, affecting hydraulic conductivity measurements
❌ Less Durable – Can be damaged in hard or rocky formations
Conclusion
Drive-point piezometers are an efficient and practical solution for short-term groundwater monitoring in environmental and hydrogeological investigations. They provide rapid, low-cost data collection, making them valuable for contaminant assessments, remediation projects, and hydrology studies. However, for long-term monitoring or deep groundwater investigations, conventional monitoring wells may be more appropriate.